The Evolution and Importance of Automobile Plastic Molds
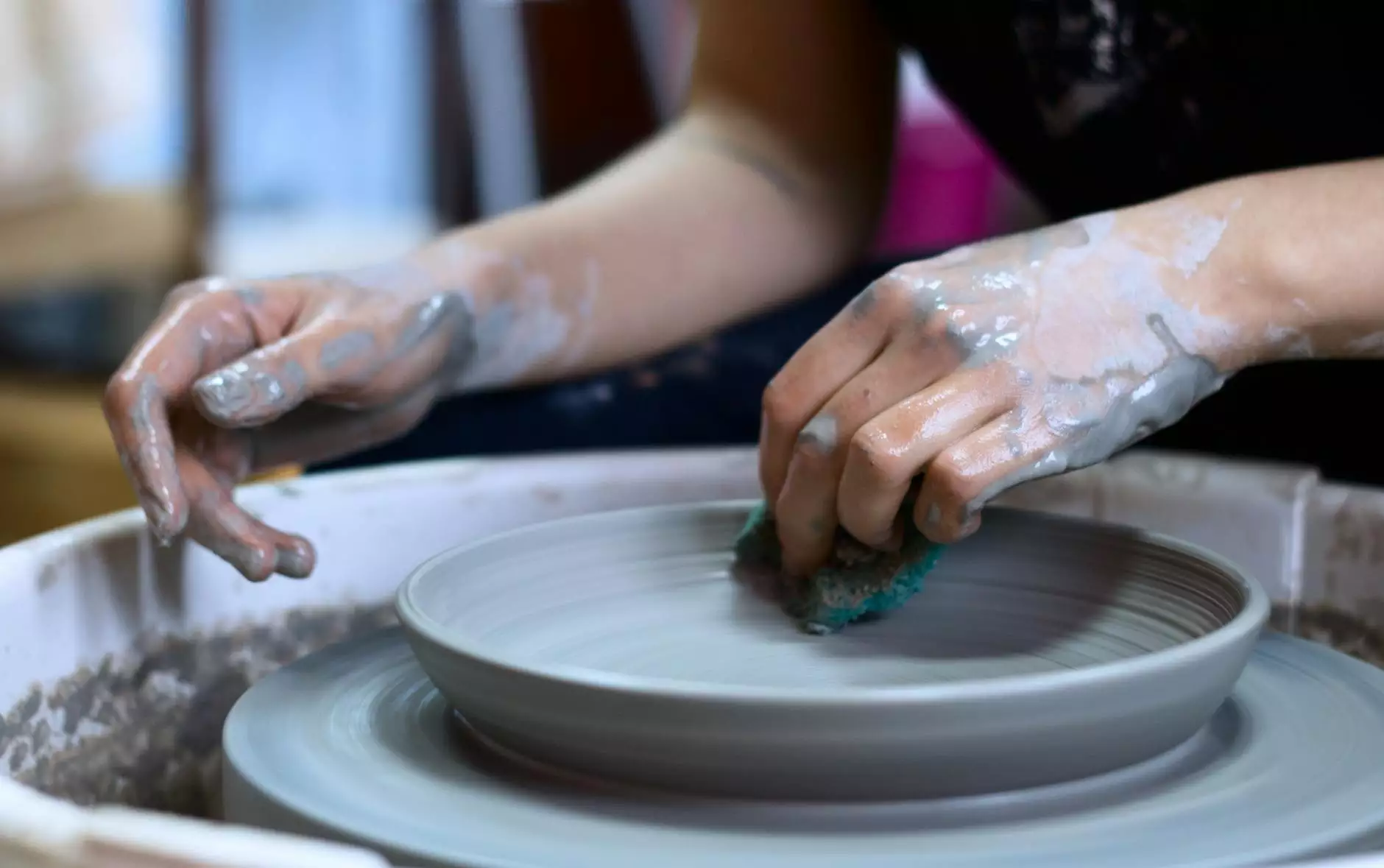
In today's fast-paced manufacturing environment, the role of automobile plastic molds cannot be overstated. As the automotive industry continues to advance, the demand for innovative and efficient production methods has led to an increased reliance on high-quality plastic molding techniques. This article delves deep into the intricate world of automobile plastic molds, exploring their significance, technological advancements, and the impact they have on the global automotive industry.
What are Automobile Plastic Molds?
Automobile plastic molds are specialized tools used to shape and form plastic materials into desired components for vehicles. These molds are crafted with precision, utilizing various types of materials such as steel or aluminum, to produce high-quality automotive parts. The process of molding involves injecting melted plastic into the mold cavity, allowing it to cool and solidify, thus creating the final product.
The Significance of Plastic Molding in Automotive Production
Plastic molding has revolutionized the automotive manufacturing landscape. Here are some of the key reasons why:
- Weight Reduction: Plastic components are significantly lighter than their metal counterparts, contributing to overall vehicle weight reduction, which enhances fuel efficiency.
- Cost-Effectiveness: The production process of plastic parts often proves to be more cost-effective, especially in high-volume manufacturing.
- Complex Shapes and Designs: The molding process allows for intricate designs that would be difficult to achieve with traditional metal fabrication methods.
- Corrosion Resistance: Plastic materials are inherently resistant to corrosion, increasing the lifespan and durability of automotive components.
Types of Plastic Used in Automobile Manufacturing
The choice of material in automobile plastic molds plays a crucial role in the performance and longevity of automotive parts. Some commonly used plastics include:
- Acrylonitrile Butadiene Styrene (ABS): Known for its toughness and impact resistance, ABS is widely used in automotive interior components.
- Polypropylene (PP): This lightweight material is ideal for exterior parts, including bumpers and fenders.
- Polycarbonate (PC): With excellent clarity and impact resistance, polycarbonate is often used for headlight lenses and other transparent components.
- Polyvinyl Chloride (PVC): PVC is commonly used in automotive wiring and fittings due to its excellent chemical resistance.
The Process of Creating Automobile Plastic Molds
The creation of automobile plastic molds involves several key stages, each essential for ensuring the quality and efficiency of the final product. These stages include:
1. Design and Engineering
The process begins with designing the mold. Skilled engineers use advanced CAD software to create a 3D model of the mold, taking into consideration factors such as shrinkage, draft angles, and cooling channels.
2. Material Selection
Choosing the right material for the mold is vital. Manufacturers typically opt for high-quality steel or aluminum, as these materials offer durability and can withstand the high temperatures involved in the molding process.
3. Machining the Mold
Once the design is finalized, the molding components are machined using CNC (Computer Numerical Control) technology. This precision machining ensures that all features of the mold are accurate and consistent.
4. Mold Assembly
The individual components of the mold are then assembled. This includes attaching the core and cavity, as well as integrating cooling lines that help regulate the temperature during the molding process.
5. Testing and Quality Assurance
Before production begins, the mold undergoes rigorous testing to ensure it meets quality standards. This phase is crucial for identifying any potential issues that could affect the final product.
Advantages of Using Automobile Plastic Molds
Utilizing automobile plastic molds offers numerous advantages to manufacturers, including:
- Faster Production Times: The injection molding process allows for rapid production of parts, significantly reducing lead times.
- Consistency and Precision: Molds produce identical parts with high precision, ensuring consistency across production runs.
- Design Flexibility: Manufacturers can easily modify mold designs to accommodate new automotive trends and technologies.
- Environmental Sustainability: Many plastics used today are recyclable, contributing to reducing landfill waste in the automotive industry.
DeepMould.net: A Leader in Automobile Plastic Molding
At DeepMould.net, we pride ourselves on being at the forefront of the automobile plastic molding industry. Our commitment to quality and innovation sets us apart from the competition. Here are some reasons why choosing DeepMould.net is the best option for your plastic molding needs:
1. Advanced Technology
We utilize the latest technologies in mold design and production, ensuring that our molds are built to the highest standards of quality and efficiency. Our state-of-the-art facilities are equipped with the latest CNC machines, CAD software, and injection molding technology.
2. Experienced Team
Our team of skilled engineers and designers brings years of experience in the automotive industry, allowing us to tackle even the most complex molding challenges with ease.
3. Custom Solutions
At DeepMould.net, we understand that every project is unique. That’s why we offer custom molding solutions tailored specifically to meet your requirements. Whether you need a prototype or a large-scale production run, we’ve got you covered.
4. Commitment to Sustainability
We are dedicated to minimizing our environmental impact. Our practices emphasize the use of recyclable materials and energy-efficient processes, ensuring a sustainable approach to manufacturing.
The Future of Automobile Plastic Molding
The future of automobile plastic molds is bright, with continuous advancements in technology and materials. As the automotive industry moves towards electric and autonomous vehicles, the demand for lightweight and efficient components will only increase.
Furthermore, innovations such as 3D printing and biodegradable plastics are expected to play a significant role in the evolution of automotive manufacturing. These developments will not only enhance production capabilities but also lead to a more sustainable industry overall.
Conclusion
In conclusion, the realm of automobile plastic molds is an integral part of the automotive industry, driving innovation and efficiency. Companies like DeepMould.net are leading the charge in providing high-quality molds that meet the ever-evolving demands of modern automotive design and manufacturing. The future holds exciting possibilities as new technologies and materials emerge, ensuring that plastic molding remains at the forefront of automotive production.
For more information about our services and how we can help you with your automotive molding needs, visit us at DeepMould.net.